Technologies
Discover, Connect & Collaborate at TECHINNOVATION 2021
Bonding of Dissimilar Materials using Nanostructures
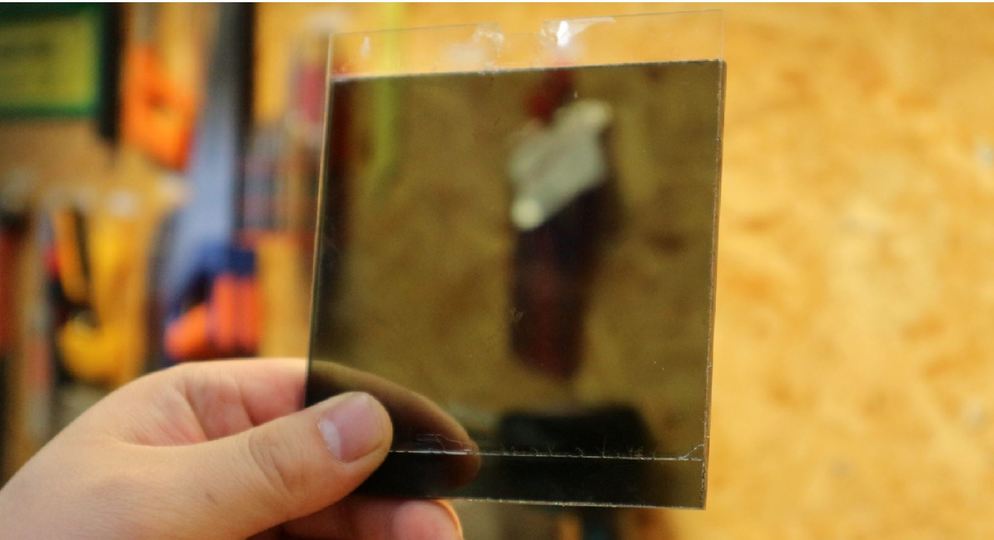
Technology Overview
Adhesives such as glues and fasteners are often used to bond similar materials. However, to join dissimilar materials such as plastics to metals often presents a challenge due to the differences in surface interfaces and inability to offer proper and strong adhesion.
This technology offers a proprietary solution to address the limitations faced during the bonding of dissimilar materials using a nanolayer formed by nanostructures known as polymer brushes. Polymeric chains from the polymer brushes can create strong bonds to the substrate, polymerising to approximately up to 50nm long. Assembly of the plastic component can be performed by direct adhesion or via conventional industrial methods such as plastic over-moulding or welding. Apart from the use of an adhesive to bond dissimilar materials, the technology may also be applied as a nanocoating to impart functional properties such as anti-fouling, hydrophobicity/hydrophilicity and for surface protection.
Technology Features, Specifications and Advantages
The technology comprises of unique chemical and physical nanostructures called polymer brushes that are invisible to the naked eye. Polymer brushes undergo a polymerisation process to form polymer chains that are tethered to a surface, allowing them to react and bond through chemical entanglements to create a polymeric nanolayer that can range from 10 to 50 nm in thickness. When applied on solid materials like metals, it allows for ultra-tight direct bonding to plastics which is unaffected by the roughness of the surface. The joining process can be incorporated in most types of traditional industrial techniques, like injection moulding and solvent or ultrasonic welding. This provides a highly efficient and versatile assembly process without the need for traditional primers or glues.
As a surface primer, the polymer brush-based nanocoating provides improved adhesion in the areas of strength, stability, lifetime, and coating ability. Surfaces pre-coated with the primer can be stored separately for many months, making it possible to separate the priming and assembly process.
By controlling the chemical and physical structure of the polymer brushes, the user is able to change the properties of the bonding surfaces and impart other functional properties including anti-fouling, hydrophobicity/hydrophilicity, surface friction etc.
Potential Applications
- Medical – A safe way to bond as there is no adhesive layer seeping out and no interface for bacteria to grow
- Electronics – Tight and strong adhesion between plastics and metals that is also stable at high temperatures
- Offshore and Marine – Anti-fouling coating against marine organisms, as the adhesion is robust enough to withstand conditions in harsh environments, watertight against biofilm
- Food and Beverage – Safe adhesion with no risk of contamination or leaking over time
Customer Benefit
- Provides strong direct bonding between otherwise incompatible materials
- Ultra-tight sealing
- Chemically safe - No environmental risks with the final products. Ideal for medical devices.
- Invisible